What is Kerui Refractory Plastic Refractory?
Kerui Refractory plastic refractory plays a crucial role in high-temperature industrial applications, offering durable and versatile solutions for lining environments. This article provides an overview of the defining properties and typical uses of plastic refractories.
What is Plastic Refractory?
Plastic refractory is a monolithic refractory that remains pliable until molded and heated to set. They consist of high-temp-resistant aggregates and fine powders mixed with plasticizers, water, and binding agents such as clay, phosphates, or aluminum silicates. Unlike refractory bricks, plastic refractories offer flexibility and ease of application, especially in complex furnace shapes or areas experiencing rapid thermal cycling.
Key Properties:
- High Thermal Resistance: Suitable for applications exceeding 1500℃.
- Good Workability: Remains moldable and easy to shape.
- Thermal Shock Resistance: Withstands abrupt temperature changes.
- Long Shelf Life: Maintains plasticity for extended periods if stored properly.
Types of Plastic Refractory
By binder and aggregate types:
- Binder Types: Common binders include phosphate, aluminum sulfate, silicate, and resin.
- Phosphate-bonded Refractories: Offer excellent strength and resistance after heat treatment, ideal for high-temperature furnaces.
- Aluminum Sulfate Binders: Provide quick-setting properties, suitable for rapid hardening situations.
By Aggregate Types: Common aggregates include clay, high-alumina, silicon carbide, mullite, and zircon.
- Clay-based Refractories: Cost-effective and widely used for moderate temperatures.
- High-alumina Refractories: Suitable for high-temperature applications due to excellent stability.
- Silicon Carbide: Known for high thermal conductivity, commonly used in furnaces with frequent temperature cycling.
Key Applications of Plastic Refractory
Plastic refractory is employed across multiple industries due to their adaptability and thermal stability:
- Metallurgical Furnaces: Used as liners for electric arc furnace roofs and ladles, resisting slag corrosion, ideal for steel and aluminum production.
- Heat Treatment Furnaces: Applied in annealing, forging, and sintering furnaces, providing stability under frequent heating and cooling cycles.
- Cement Kilns: Essential for extreme temperatures and mechanical wear, helping maintain protective linings.
- Petrochemical Furnaces: Resists chemical corrosion from sulfur compounds and acids prevalent in petrochemical processes.
Distinguishing Characteristics of Plastic Refractory
Several features set plastic refractory apart:
- Plasticity and Moldability: Ready-to-apply materials ideal for complex shapes and repairs.
- Thermal Shock Resistance: Withstands frequent temperature fluctuations without cracking.
- Mechanical Strength and Durability: Exhibits robust compressive strength, enhancing performance in high-wear conditions.
Selecting the Right Plastic Refractory
When choosing a plastic refractory, consider:
- Operational Temperature: Ensure the material withstands the maximum service temperature.
- Type of Environment: Select materials with enhanced corrosion resistance for slag or corrosive atmospheres.
- Application Method: Look for flexibility and moldability for complex shapes or repairs.
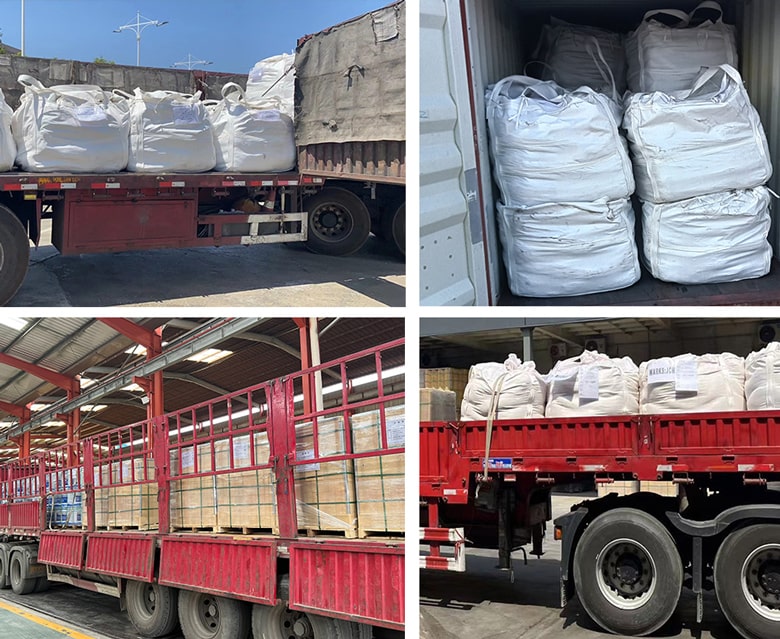
Conclusion
Plastic refractory is vital in high-temp industries, offering versatility, durability, and thermal shock resistance. With the continuous development of plastic refractory, they have evolved to be more adaptable and efficient. If you need customized plastic refractory suitable for your project, please contact Kerui Refractory.