Magnesia Refractory Bricks
As an important consumable in refractory industry, magnesia refractory bricks are in great need. This brick is commonly made of multi minerals and has strong alkaline and high density. Kerui is a reliable manufacturer with 20 years of experience.
-
89-97.5%
MgO (≥)
-
2.85-3.00g/cm³
Bulk Density
-
1500-1700℃
Refractoriness Under Load
-
50-60MPa
Cold Crushing Strength
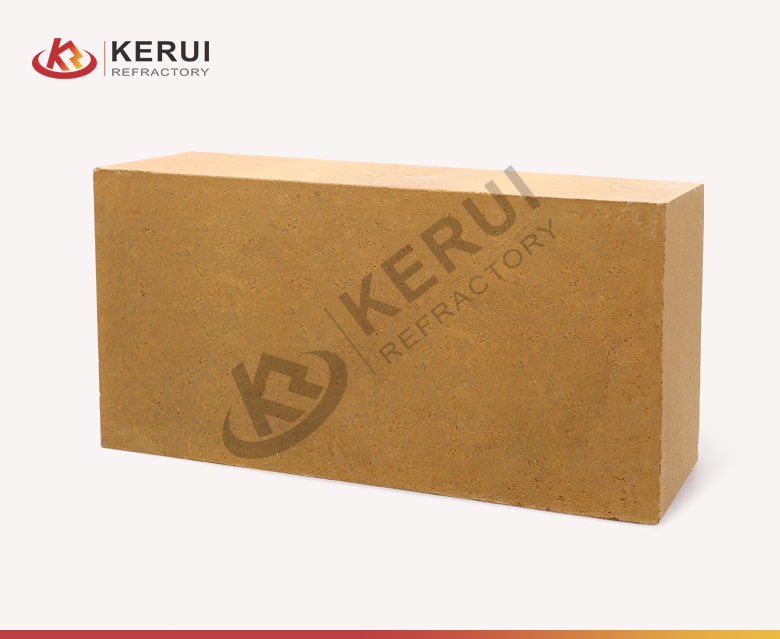
Parameters of Kerui Magnesia Refractory Brick
The biggest difference among each kind of magnesia brick for sale is the content of MgO. Therefore, in line with the parameters and your specific demands, you can find suitable magnesium oxide bricks for your project. Contact Kerui to receive more information.
Item/Grade | M-98 | M-97A | M-97B | M-95A | M-95B | M-91 | M-89 | |
---|---|---|---|---|---|---|---|---|
ω (MgO)/% | μ0 ≥ | 97.5 | 97.0 | 96.5 | 95.0 | 94.5 | 91.0 | 89.0 |
σ | 1.0 | 1.5 | ||||||
ω (SiO2)/% | μ0 ≤ | 1.00 | 1.20 | 1.50 | 2.00 | 2.50 | / | / |
σ | 0.30 | |||||||
ω (CaO)/% | μ0 ≤ | / | / | / | 2.00 | 2.00 | 3.00 | 3.00 |
σ | 0.30 | |||||||
Apparent Porosity/% | μ0 ≤ | 16 | 16 | 18 | 16 | 18 | 18 | 20 |
σ | 1.5 | |||||||
Bulk Density (g/cm³) | μ0 ≥ | 3.00 | 3.00 | 2.95 | 2.90 | 2.85 | ||
σ | 0.30 | |||||||
Cold Crushing Strength/MPa | μ0 ≥ | 60 | 60 | 60 | 60 | 50 | ||
Xmin | 50 | 50 | 50 | 50 | 45 | |||
σ | 10 | |||||||
0.2MPa Refractoriness Underload/℃ | μ0 ≥ | 1700 | 1700 | 1650 | 1560 | 1500 | ||
σ | 15 | |||||||
Permanent Linear Change/% | Xmin~Xmax | 1650℃*2h -0.2-0 | 1650℃*2h -0.3-0 | 1600℃*2h -0.5-0 | 1600℃*2h -0.6-0 |
Introduction of Kerui Magnesia Refractory Bricks
The main raw material of Kerui magnesia bricks is magnesia (MgO), with a content as high as 91%. Meanwhile, it has high refractoriness at 2000℃ (3632℉) and strong resistance to alkaline corrosion. Besides, Kerui offers large-scale magnesite refractory bricks for sale continuously. Addtionally, according to different manufacturing processes, Kerui magnesium brick can be classified into burnt refractory brick and unburnt refractory brick:
Burnt Magnesia Refractory Bricks
Burnt magnesia brick needs sintering process with high temperatures to combine particles in the bricks tightly. Therefore, this brick has higher density and durability. Generally, burnt magnesia in brick includes magnesia refractory brick, magnesia chrome brick, magnesia calcium brick, magnesia alumina spinel brick, magnesia iron brick and so on.
Unburnt Magnesia Refractory Bricks
Unburnt magnesia brick adapts chemical or physical reactions to form a dense structure. Meanwhile, it has a shorter production cycle and lower magnesite bricks price. Commonly unburnt magnesia brick includes magnesia carbon brick, alumina magnesia carbon brick, alumina silica carbon brick, magnesia calcium carbon brick and so on.
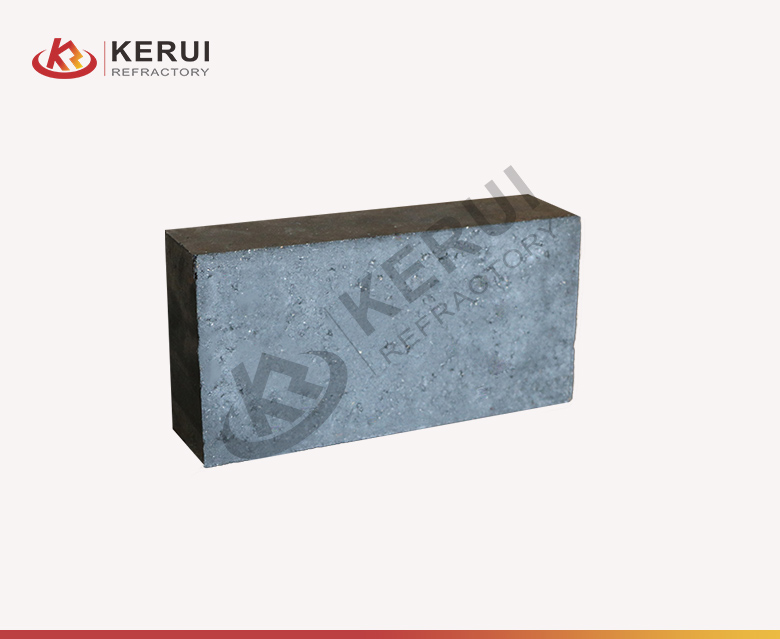
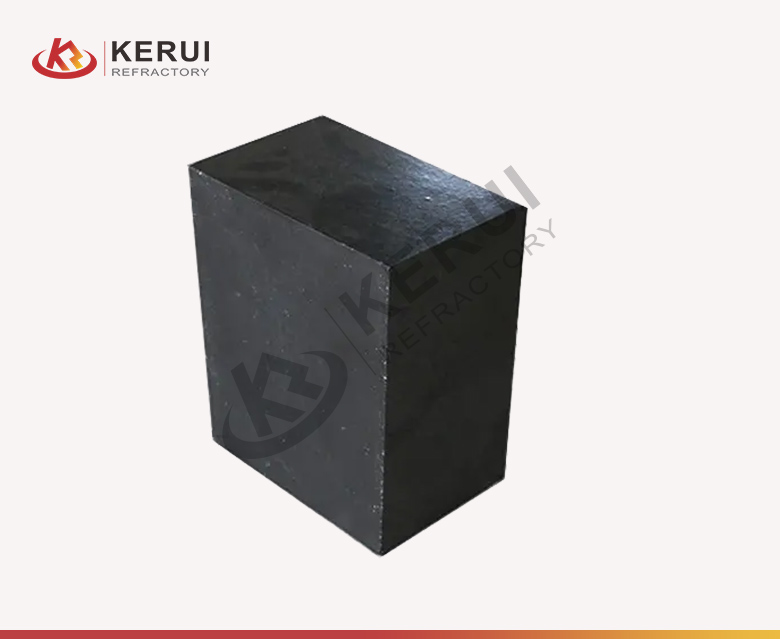
Magnesite Bricks Manufacturing Process
Features of Kerui Magnesia Refractory Bricks
As the main content of magnesium brick, MgO has high melting point, which results in high refractoriness. Besides, Kerui factory is located in Xinmi City, Henan Province, it owns rich mineral resources for refractory materials. Therefore, Kerui magnesia bricks properties have superior perforance.
Flexible magnesia brick can be cut and installed easily to fit various complex shapes and structural needs. Besides, magnesite bricks are relatively lighter than other refractory bricks, which is convenient for workers to carry and operate. Therefore, you can contact Kerui to customize magnesia brick to save your time and energy on cutting.
Kerui magnesia brick has strong thermal conductivity. Meanwhile, this means that magnesite bricks is able to absorb and release heat quickly, which improves working efficiency and heat energy utilization. Additionally, by using magnesia fire resistance brick in your kilns, the heat can spread soon and reduce energy consumption.
Compared with magnesia refractory bricks from other suppliers, Kerui’s brick uses better raw materials and more advanced production technology. Therefore, Kerui magnesium brick is harder and has higher density. At the same time, customers who invest in Kerui magnesium brick can reduce the frequency of replacement.
Functions of Magnesia Refractory Bricks
Steel and Iron Industry
- Steel melting furnace lining;
- The ferroalloy fiber cable furnace;
- Basic open-hearth furnace;
- Hyperthermia tunnel kiln;
- Permanent layers in steel making converters, AOD furnaces;
- Steel ladles and BOF;
- Other parts of steel and iron furnace;
Cement Industry
- Lining of rotary cement kiln;
- Bottom and wall of heating furnace;
- Lime kilns;
- Calcination kiln;
- shaft kiln;
- other parts of cement kilns;
Non-ferrous Industry
- Slag line;
- Linings of copper, lead, zinc, tin furnace;
- Tapping hole of metal mixer furnaces
- Other parts of non-ferrous furnaces;
Glass Industry
- Chimney block;
- Regenerative chamber;
- Flue and combustion chamber;
- Other parts of glass furnace.
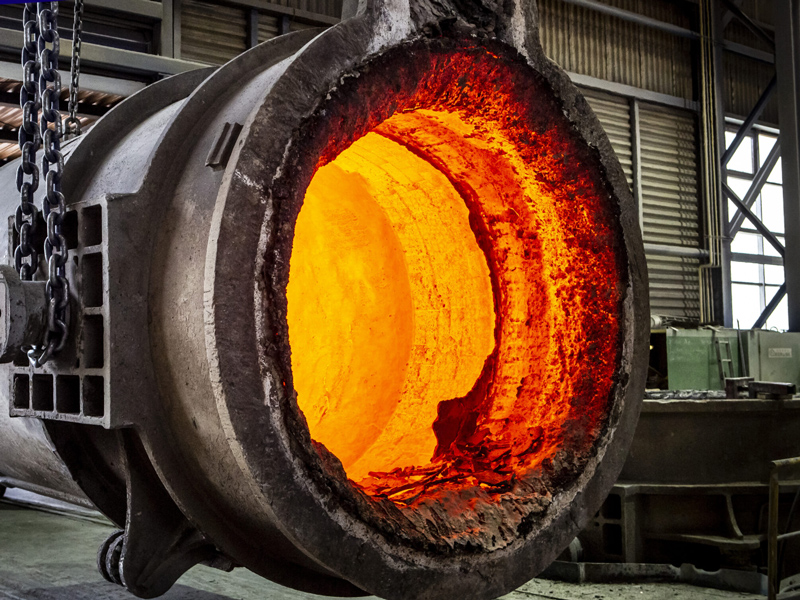
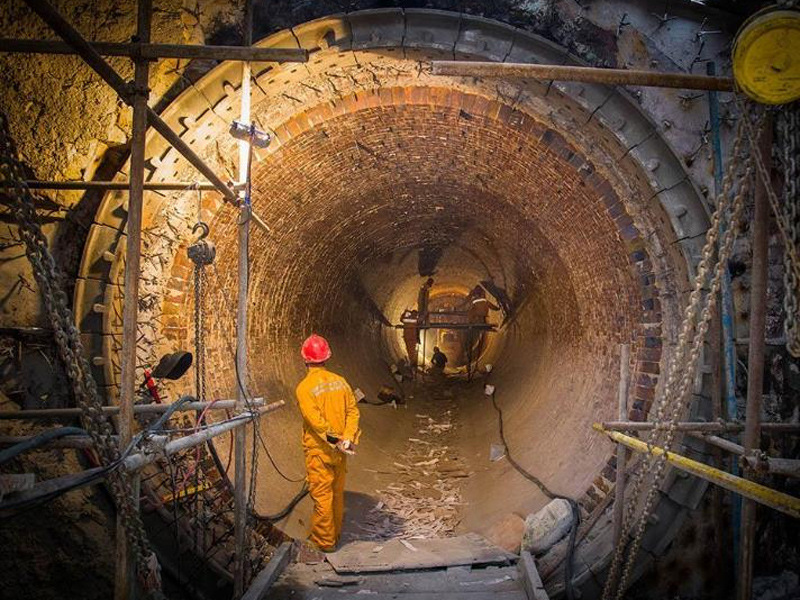
Kerui Magnesia Refractory Bricks Price
Kerui magnesite brick price is determined according to the product performance, specifications, quantity, etc. required by customers. So if you want to get a detailed refractory brick price list, please tell Kerui your detailed requirements. Then compared with the same industry, Kerui offers more reasonable magnesite bricks prices. Because we are the original magnesia bricks manufacturer. Besides, Kerui factory is located in Xinmi City, Henan Province, which is rich in mineral resources. This basic refractory bricks consist of high quality materials. Moreover, Kerui’s lower production cost has brought about a fair price for magnesia bricks.
Meanwhile, if you want to get a detailed quotation for magnesium bricks immediately, we recommend you provide the following information:
Each high temperature kiln has different characteristics and operational requirements. Thus, according to the information you provide, magnesia brick supplier can estimate the working temperature, chemical environment and other information in a short time. Therefore, you can get products that suits your project.
The corner of high temperature kilns may need magnesia brick with high resistance to corrosion. Meanwhile, the bottom of kilns may need magnesium brick with higher refractoriness. In conclusion, there may be differences in formula, material and fire bricks manufacturing in different parts.
Based on your purchasing volumes, magnesite brick manufacturers are able to accurately calculate material and production costs to realize accurate magnesite bricks properties. Thus they can provide you with quotations reflecting economies of scale or any volume-based discounts that may apply.
A clear purchase budget promotes the negotiation process. So it is helpful for magnesium brick suppliers to provide a quote within your financial expectations. Additionally, it’s highly efficient to tell Kerui about your estimated budget to get suitable kind of magnesite refractory bricks.
The magnesium oxide bricks suppliers need to arrange production plans and material supply chains according to delivery deadlines. Meanwhile, knowing your delivery deadlines in advance can help suppliers deploy the necessary resources and ensure smooth production and delivery.
Customized magnesia brick may cost a little more. Besides, the brick also brings more benefits to your project. No matter whether you have special requirements on colors, shapes, chemical compositions, marks on final products or other aspect, Kerui is confident to satisfy.
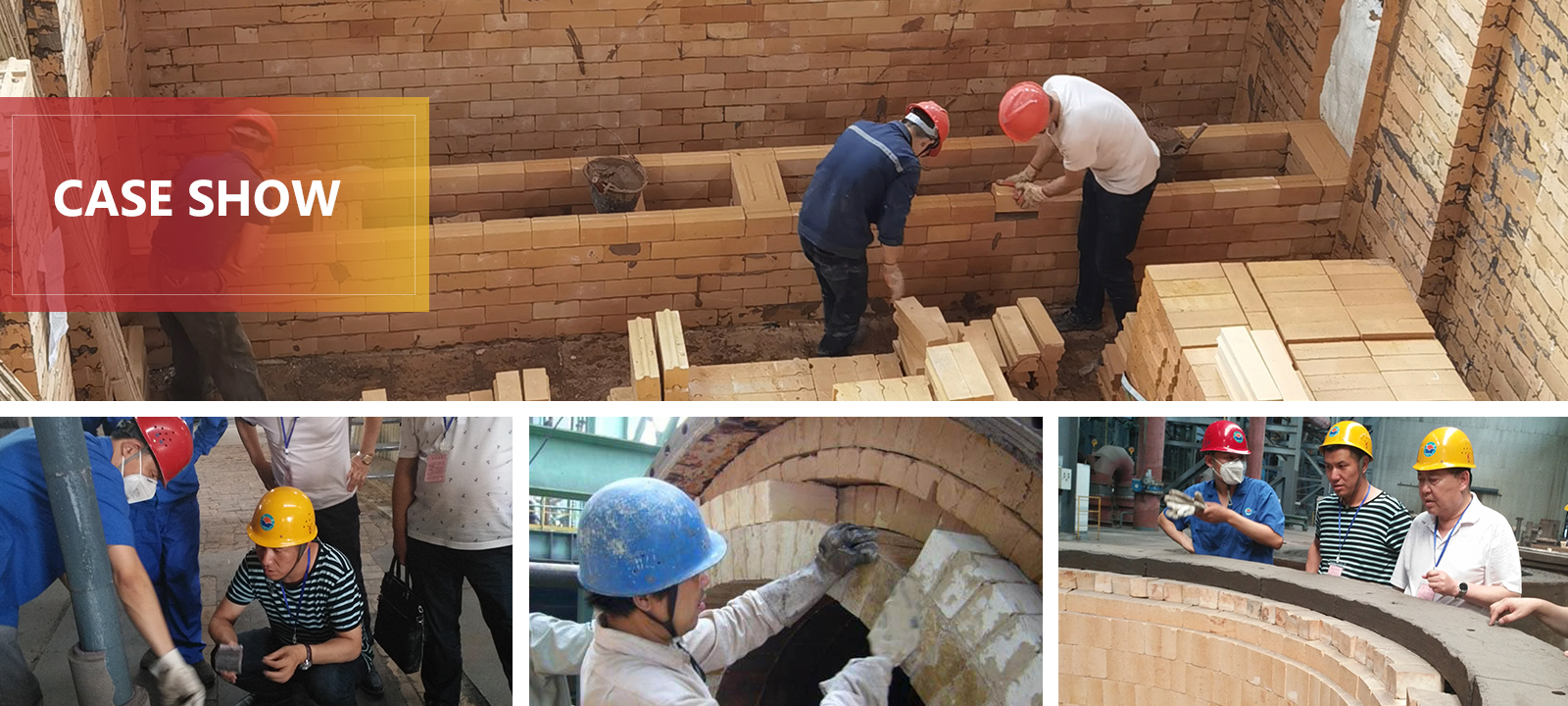
All in all, Kerui magnesia brick has been used in various fields. Therefore, it’s crucial for customers to choose high quality magnesia brick from reliable manufacturers. If you’re looking for good magnesia brick with favorable price, please contact Kerui now!