Fire brick is also known as refractory brick. From the name we can know it’s a kind of brick that can withstand extremely high temperatures. Fire bricks are bricks used in high temperature environments. Usually customers buy refractory bricks to be used in the lining of various kilns. As the first layer inside the kiln, this kind of working environment also requires refractory bricks to have other excellent characteristics, such as to withstand rapid temperature changes, to withstand the erosion of chemicals or slag, and so on.
Can Any Brick Be Used as A Fire Brick?
No! It’s not that any brick can be used as a fire brick. Ordinary bricks cannot withstand high temperatures and usually begin to decompose at around 1000°C(1832℉). Fire brick is specially designed to withstand high temperatures up to 1790°C(3254℉).
Additionally, the porosity of fire bricks affects the ability to store fuel and release it slowly to maintain steady combustion in these types of applications. Therefore fire brick should always be used when constructing an area that will face exposure to extreme temperatures. Its composition determines the high refractoriness and other properties of fire brick.
Analysis of Compositions of Fire Brick
Main components of making fire bricks are fire lay, binders, all kinds of quartz, dolomite, zircon, spinel and more.
Al2O3:
Alumina is the main material that determines refractoriness and hardness of fire bricks. Generally, the high purity it contains, the more expensive fire brick is. According to different contents of Al2O3, we rank common alumina fire bricks as follows:
Content of Al2O3: corundum brick > corundum mullite brick > mullite brick > high alumina brick > fire clay brick.
SiO2
As a kind of acid material, fire bricks that take SiO2 as the main raw material have strong corrosion to acid corrosion. Besides, high content of SiO2 brings good wear resistance and heat storage capacity. According to the different contents of SiO2, here are few types of silica brick:
Content of SiO2: silica brick > half silica brick.
MgO
The magnesia is a kind of alkaline material, which brings good resistance to basic corrosion and good thermal stability. Almost all kinds of bricks with MgO have high refractoriness. Besides, this brick also brings good chemical resistance in many industrial kilns.
Content of MgO: magnesia brick > magnesia spinel brick > magnesia carbon brick > magnesia chrome brick.
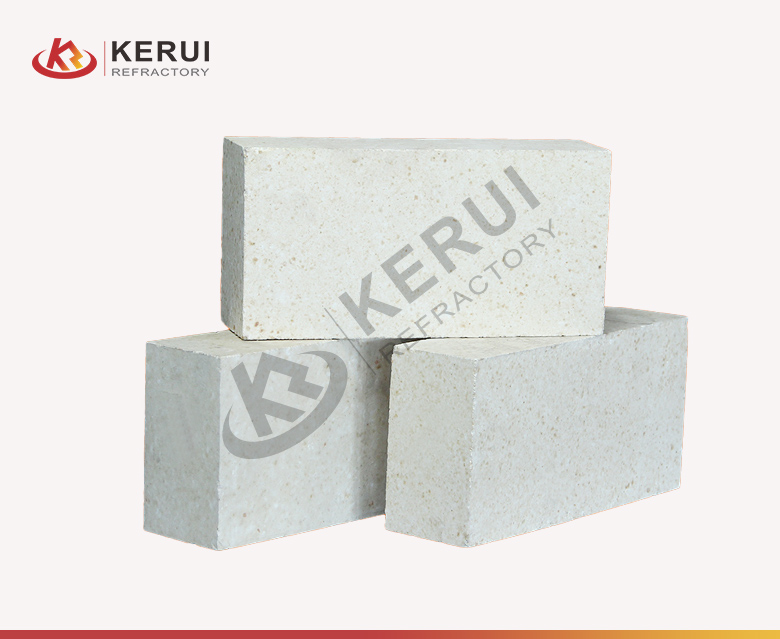
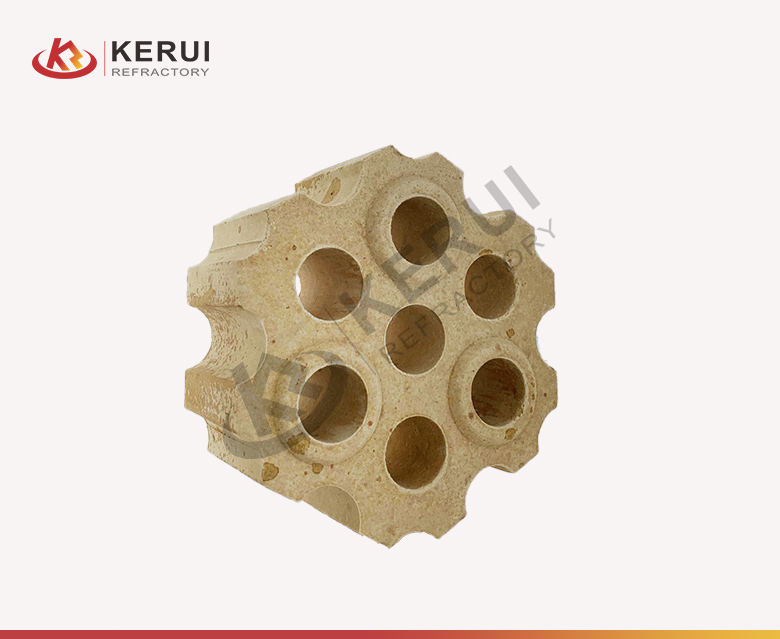
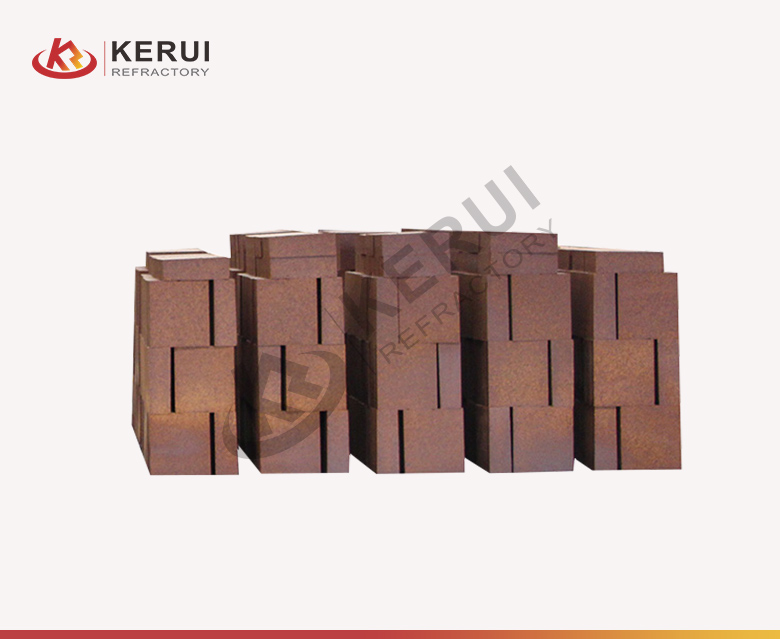
How is Fire Brick Made?
In order to obtain high temperature resistance, Kerui must strictly control the production process to meet or exceed industry standards. The manufacturing process of fire bricks involves several steps, including material preparation, shaping, drying, and firing. The key steps are as follows:
Material Preparation
The raw materials, such as clay and alumina, are carefully selected and blended to achieve the desired composition. This mixture is then ground to a fine powder, ensuring even distribution of the various components. Kerui uses fully automatic batching system to control the accurate ratio of raw materials.
Molding
The powdered mixture is mixed with water to form a plastic mass, which is then shaped into bricks using molds or extrusion. The shaped bricks are dried to remove excess moisture. There are more than 20 sets of press machines to mold fire bricks in Kerui.
Drying
The fire bricks are dried slowly to prevent cracking or warping. This is usually done in a controlled environment, such as a drying chamber, to ensure uniform drying. Kerui adopts lower temperature in drier kiln to avoid crack of fire bricks.
Sintering
To improve the density of refractory bricks, dried bricks will be sinterted at high temperature. Sintering kiln is controlled by PLC system to control real-time position and temperature of each fire brick. This results in consistent quality of fire bricks.
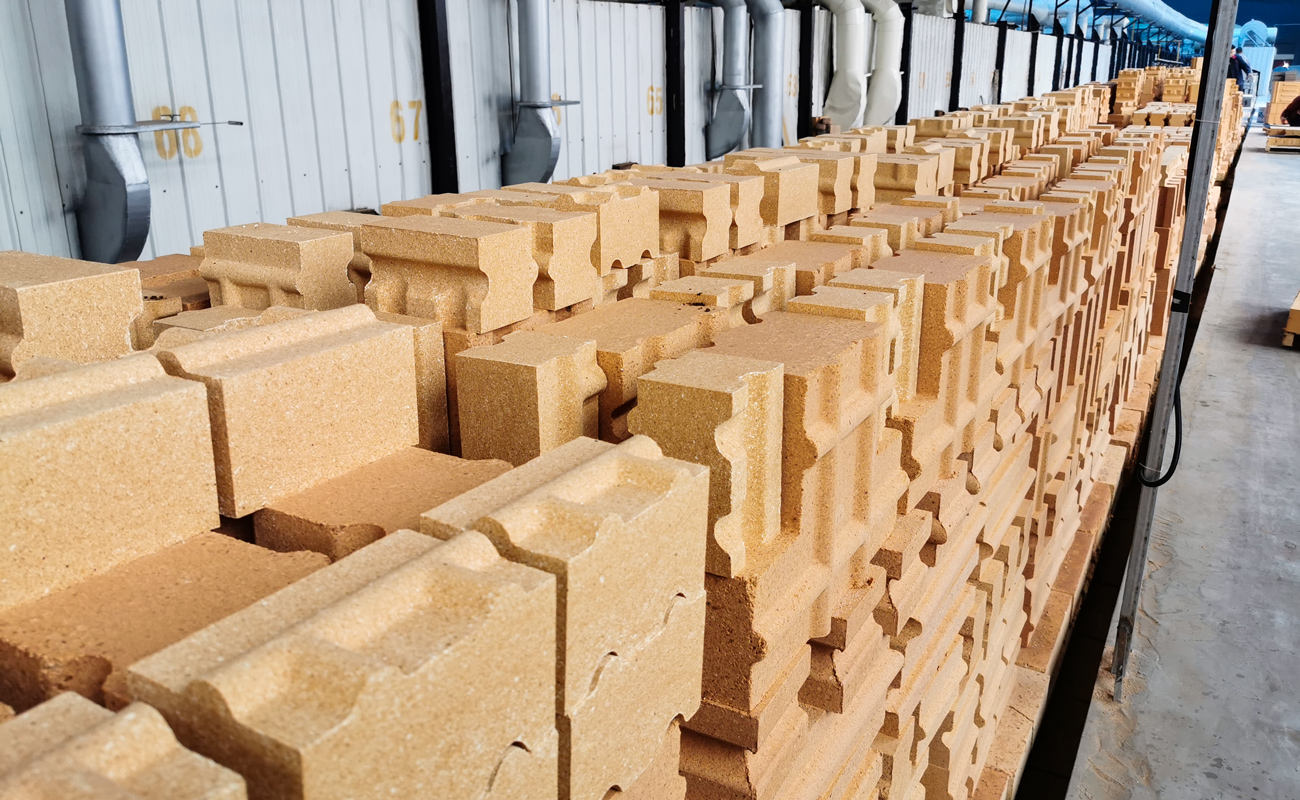
How to Use Fire Bricks?
In nowadays industry, fire bricks have wide applications. For example, Kerui fire bricks can be used as different parts of high temperature kilns in various industries. Now let me introduce in detail:
Kerui fire brick is suitable for some key parts of high temperature kilns, for example, linings, corners, walls, roofs, bottom of kilns or furnaces. When used in furnace linings, you’d better choose fire brick with high refractoriness. When used in corners of furnaces, we recommend customers choose fire bricks with strong slag resistance and chemical corrosion. No matter you plan to use fire brick in which positions, Kerui offers professional guidance and high-quality fire bricks. With good feedback of customers, Kerui fire brick is considered as products with stable performance and long service life.
In many high temperature industries, customers prefer Kerui fire retardant bricks. For example, steel and iron industry, glass industry, petrochemical industry, cement industry, building materials industry, non-ferrous industry, power industry, environmentally friendly industry and so on. There are fire bricks with superior performances in Kerui Refractory. Customers in glass industry can choose Kerui AZS brick which can resistant glass liquor and other chemical corrosion. Customers in cement industry are suitable for Kerui magnesia bricks to form a protective layer on the face of cement kiln… All in all, Kerui will offer the most suitable fire bricks for your project!
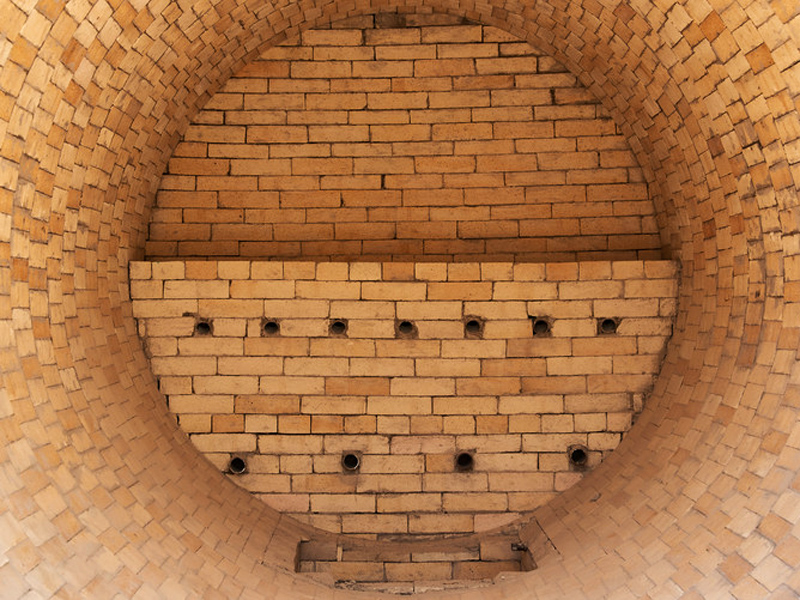
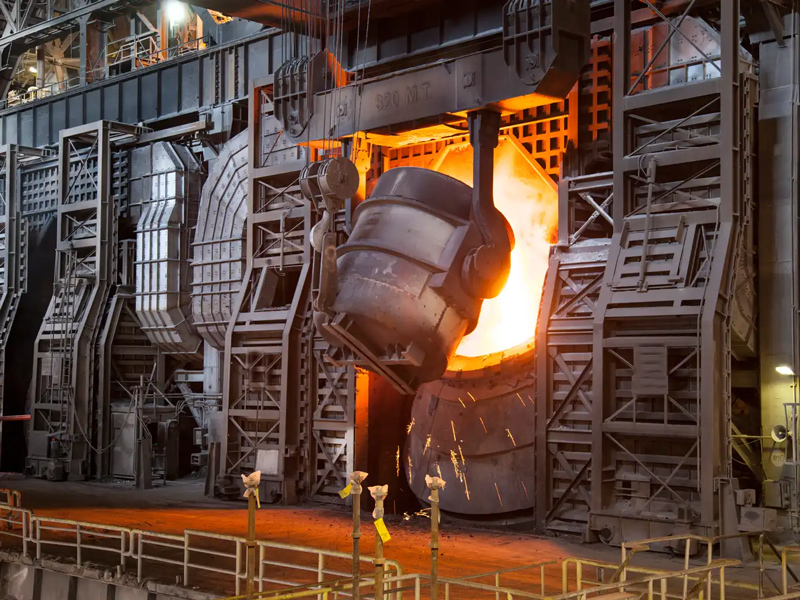
Conclusion
Fire bricks are vital materials for the construction of high temperature kilns. It’s necessary to learn about what is fire bricks in detail. This article introduces fire bricks on basis. If you still have other problems, welcome to contact Kerui and receive one-to-one consultation!