The important performances are crucial for the selection of refractory products. This can help you choose a suitable kind of refractory material for your kilns and furnaces. Now Kerui offers a complete guide on the important performances of all kinds of high temperature products. Read to know more about the 18 important performances.
Performance of High Temperatures
Refractoriness refers to the ability to resist high temperature without melting under any load. This is the basic scale and technical index to measure the ability of refractory materials to withstand high temperatures. The determination of refractory degree is to compare the temperature measuring equipment with a known refractory standard. Besides, the temperature measuring equipment of the material is being tested under specified heating conditions. We use the standard of bending at the same time to express the refractory degree. It is worth noting that the refractory degree is not the melting point of the high temperature refractory. It donesn’t represent its actual use temperature. Generally speaking, the actual operating temperature is lower than the experimentally derived refractoriness.
The corresponding temperature at which refractory materials deform to varying degrees under high temperature and constant load is called the load softening temperature. This indicator is an important indicator to characterize the structural hardness of refractory materials at high temperatures and is also an important basis for determining the service temperature of refractory materials. Because at the actual construction site, the refractory bricks will continue to bear a certain amount of pressure when they are laid together. Kerui Physics Laboratory will give the most accurate measurement results. Here you can find refractory bricks with a load softening temperature of 1200-1790°C.
During kiln operation, extreme cold and hot temperature changes are inevitable. The performance of not being damaged in the face of rapid changes in temperature is called thermal shock stability. When the temperature changes, refractory fire bricks will also expand and contract, which results in thermal stress throughout the product. It is worth noting that when thermal stress exceeds the critical temperature of the refractory material, spalling or cracking may occur. Thermal shock stability is generally measured by the number of times it can be repeatedly heated and cooled without damage.
Refractory materials are often used in extremely high temperatures. In addition to the expansion and contraction changes mentioned earlier, customers may also encounter irreversible physical and chemical reactions such as recrystallization, sintering, and crystal phase changes of refractory materials during use. When the volume of refractory products changes, the strength of the kiln will also be seriously affected, and may even cause cracking or collapse. Generally, we use the method of repeatedly sintering refractory bricks to observe their volume change rate.
Chemical attack is one of the main factors leading to the damage of refractory materials. However, it is inevitable because refractory materials are indispensable materials in industrial kilns such as glass kilns, cement kilns, and steel kilns. In fact, the chemical corrosion mechanism of refractory materials is very complex, including chemical effects such as erosion, friction, penetration, diffusion and dissolution. During the experiment, Kerui compared the corrosion depth before and after the sample of fire brick to determine the chemical corrosion resistance of the product.
Performance of the Macro Structure
By calculating the ratio of the pore volume to the total volume in a refractory material, we can derive its porosity. This indicator is the main factor in determining the density of refractory products. This value will affect many properties of refractory products or insulation products, such as thermal conductivity, specific heat capacity, normal temperature compressive strength, high temperature structural strength, thermal shock stability and slag resistance, etc. Related to this indicator are true porosity, apparent porosity, closed porosity, etc. The one we most commonly use is apparent porosity.
Bulk density refers to the mass per unit volume including all pores, generally expressed in g/cm³ or kg/m³. This indicator is one of the main indicators indicating the density of refractory materials. Correspondingly, the higher the bulk density, the fewer pores, the higher the density of the product and the higher the fire resistance. However, customers also need to judge the required volume density of refractory materials as well as fire resistance bricks based on actual construction conditions. Of course, you can also contact the Kerui technical team to customize the performance of this product for you.
In fact, the true density refers to the mass per unit volume excluding pores, that is, the ratio of the mass of the porous body to the true volume, expressed in g/cm³. True volume refers to the volume of solid material in a porous body. True density cannot reflect the macroscopic structural characteristics of the product, but it can reflect the purity and sintering degree of the raw material or product, so it is also an important technical indicator to measure the quality of some refractory products.
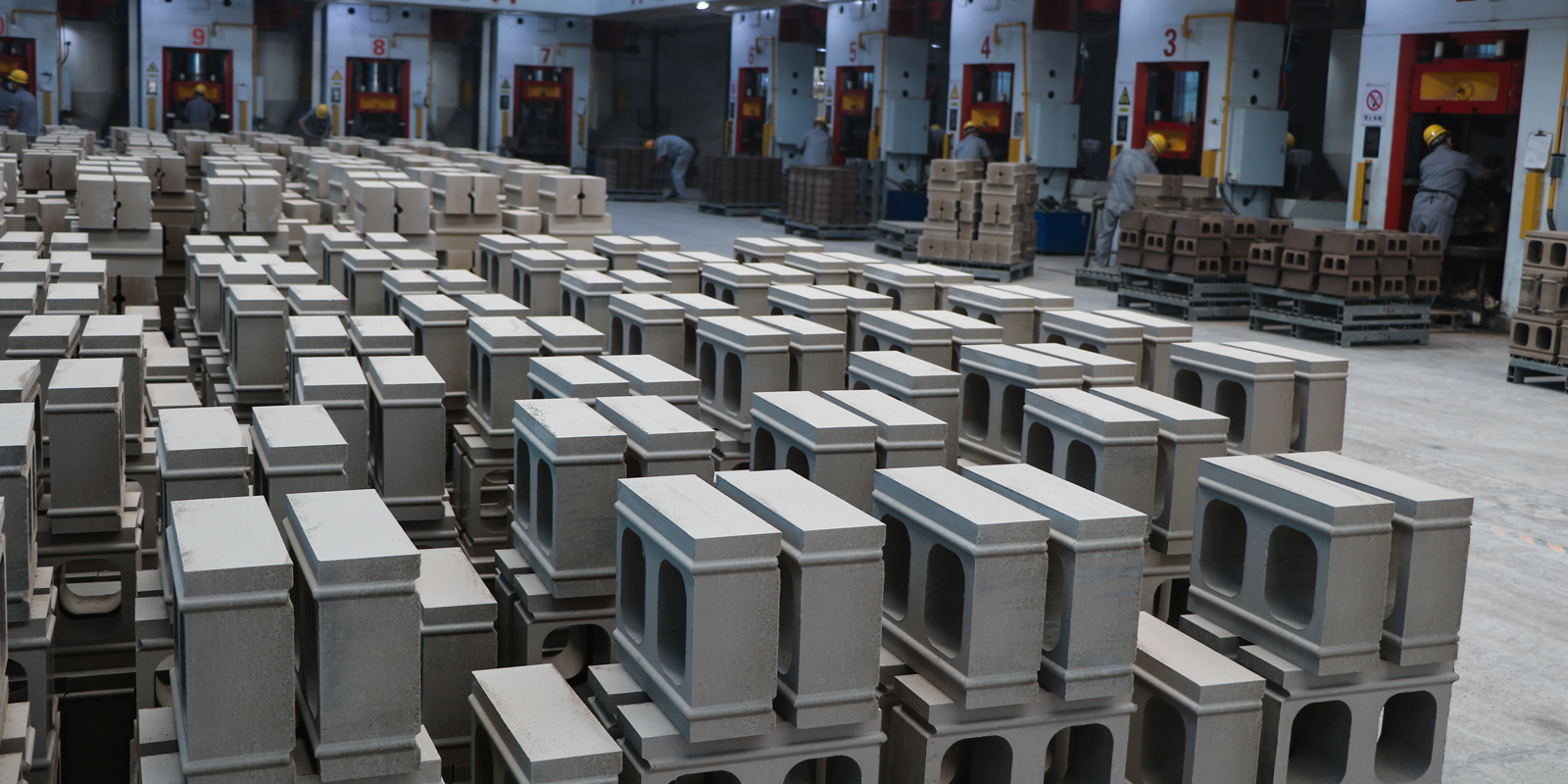
Performance of Mechanical Properties
Compressive strength refers to the maximum pressure that the product can withstand per unit area, generally expressed in MPa. Compressive strength is divided into normal temperature compressive strength, drying compressive strength, high temperature compressive strength and sintering compressive strength. Mechanical properties of these products under various conditions of use. This indicator is an important technical indicator to measure the quality and performance of refractory materials under various usage conditions. As a professional corundum brick manufacturer, Kerui offers refractory products with good comprehensive strength.
Flexural strength refers to the ultimate bending stress that can be endured per unit area. Through various physical and chemical experiments, we can determine the ability of refractory materials to resist bending or breaking under various circumstances. Similarly, flexural strength is also divided into room temperature flexural strength, drying flexural strength, high temperature flexural strength, sintering flexural strength, etc.
This indicator is defined as the ratio of stress to the strain of an object in that direction under the action of unidirectional stress. Generally speaking, if a certain force is applied to the physical object, it will undergo a certain deformation. The elastic modulus is an indicator of the stiffness of refractory ceramic fiber insulation material. From a macro perspective, elastic modulus is a measure of the product’s ability to resist elastic deformation.
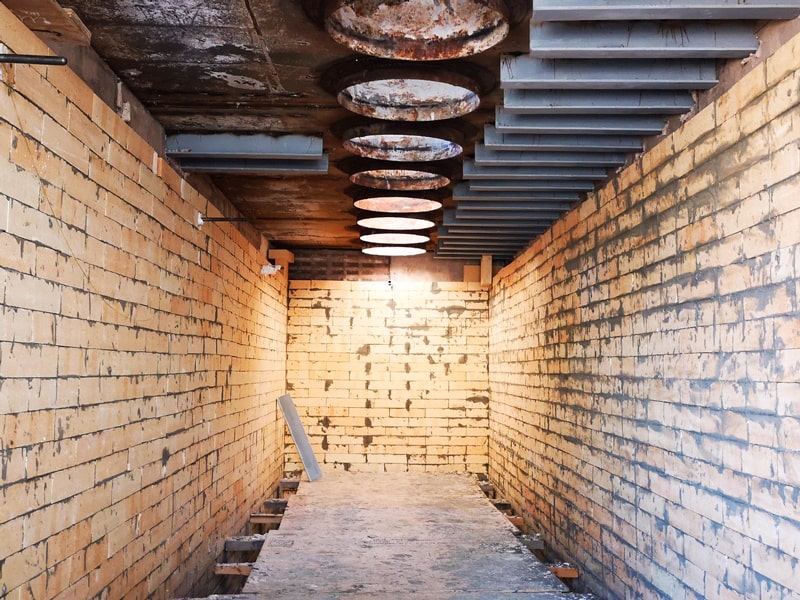
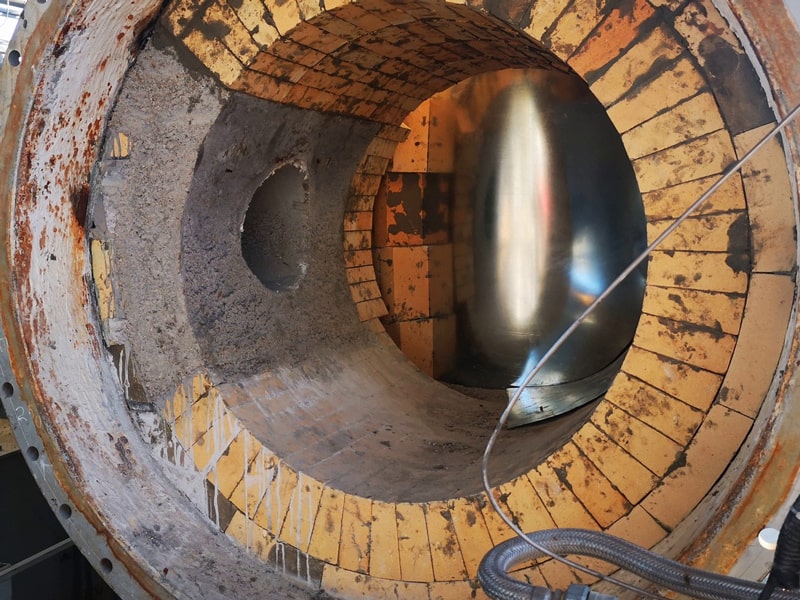
Performance of Thermal Properties
Thermal conductivity represents the ability of the refractory material to conduct heat. It is related to the properties, organizational structure and service temperature of refractory products. The unit of thermal conductivity is W/(m*k), which represents the heat flow rate through this area under unit temperature gradient. This parameter is the main parameter for calculating the lining thickness or heat loss of industrial kilns and thermal equipment. Generally speaking, customers need to pay extra attention when choosing insulation products.
The heat required for a refractory material to rise by 1°C under a specified weight and normal pressure is called specific heat capacity. The unit of specific heat capacity is kJ/(kg*K). Likewise, products with higher specific heat capacities can tolerate higher temperatures without damage. Refractory products as well as soft fire brick for sale with low specific heat capacity cannot withstand rapid cooling and heating temperature changes for a long time. This is one of the important parameters for calculation and design of thermal processes and thermal systems of thermal equipment.
Thermal expansion refers to the increase in the volume of refractory materials as the temperature increases. Due to the principle of thermal expansion and contraction, the thermal expansion of refractory materials is reversible. This also means that when the temperature returns to its original state, the length and volume of the material will also return to its original dimensions. It is worth noting that the greater the thermal expansion of the refractory material, the greater the thermal stress generated internally. It is prone to peeling when used in an environment with changing temperatures. Thermal expansion is the basis for determining the expansion joints in the kiln and formulating the thermal system.
The linear change rate of reburning is also called the residual linear expansion rate or shrinkage rate. When measuring this indicator of refractory products, the refractory product needs to be heated to a specified temperature and maintained for a period of time, then cooled to the initial temperature, and the percentage of linear expansion or linear contraction of the change is measured. Generally speaking, refractory bricks like high alumina fire brick with a low refire line change rate can maintain the stability of the kiln well.
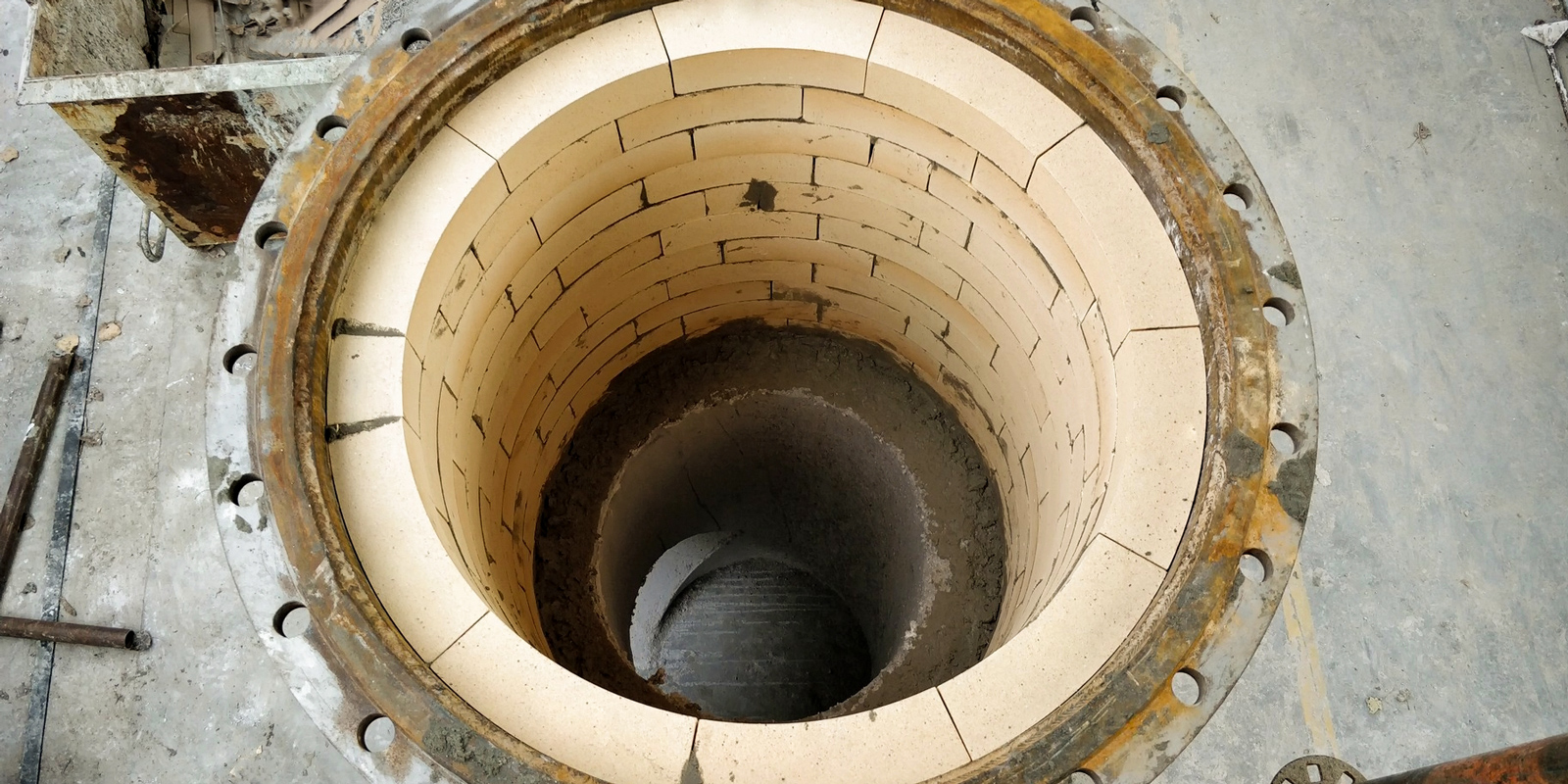
Other Performances
The plasticity number is generally used as a measure of unshaped refractory products. Besides, the plasticity number or index refers to the ability of the product to deform easily without being damaged after being stressed. This index can be obtained by comparing the deformation height of the product after impact with the height of the original sample. The plasticity index of refractory castable is generally required to be between 15% and 40%; if it is less than 15%, it will be difficult to construct and form; if it is greater than 40%, it will cause poor tamping and large shrinkage later. The way to judge the plasticity of unshaped products is that they can be kneaded into a ball by hand, and no water will leak out or touch your hands.
The percentage of slag ball content ball ratio is the content of slag balls per unit weight of refractory fiber products. This is an important performance indicator for measuring refractory fiber products. Slag balls directly affect the quality of ceramic fiber products. As the slag ball rate increases, the high density ceramic fiber board will increase and their thermal conductivity and heat demand will also increase.
Wind erosion resistance refers to the ability of refractory fiber products to resist air erosion. This parameter is expressed in terms of the airflow velocity when the airflow is damaged, and the measurement unit is m/s. When customers apply refractory fiber products in industrial furnaces with high flow rates, they are often damaged by airflow erosion. Therefore, when choosing refractory fiber products, customers should pay attention to its wind erosion resistance.
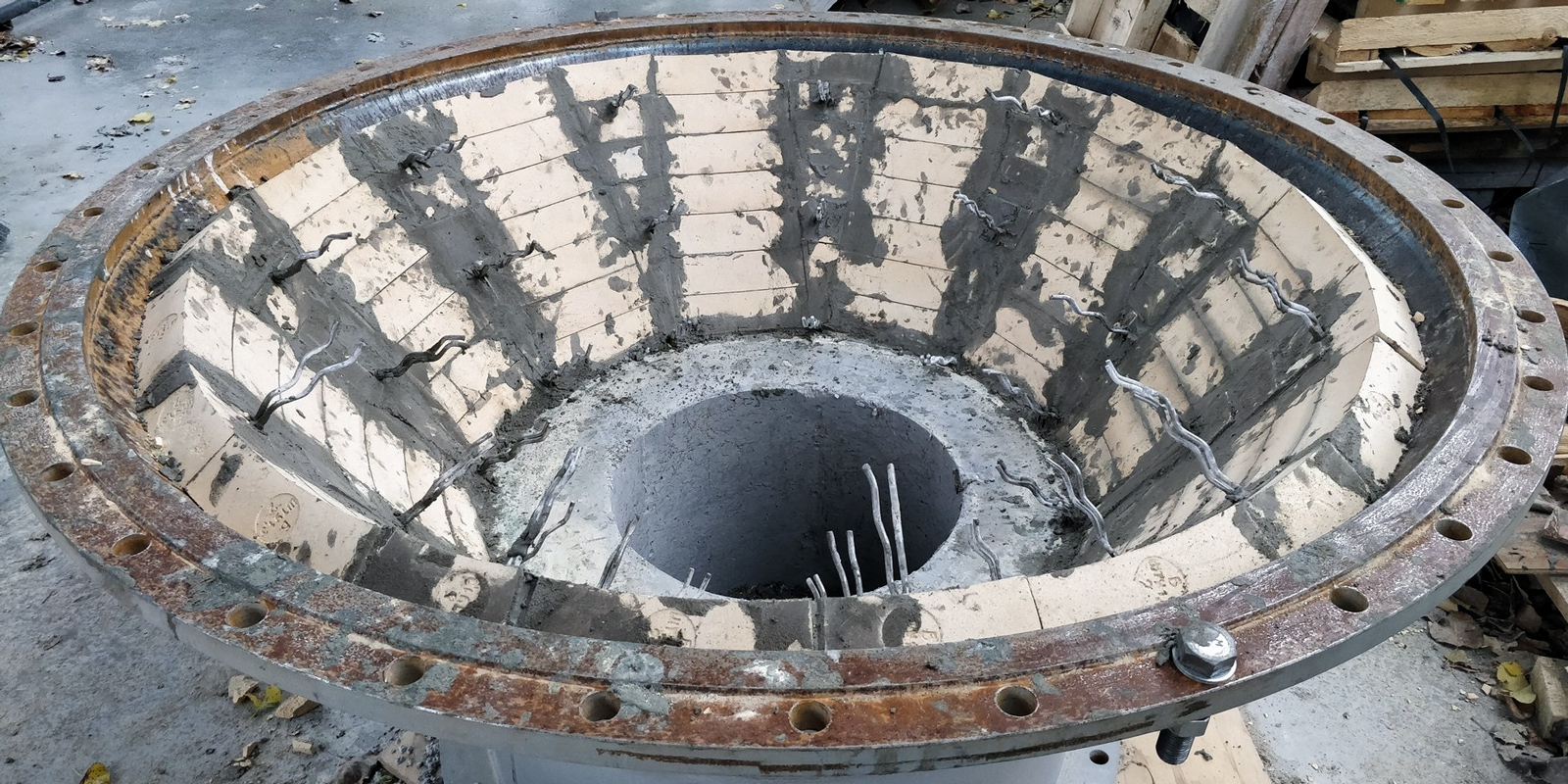
Conclusion
The above is important reference information summarized by Kerui professional team. I hope it will be useful when you choose refractory fire products. If you are looking for a reliable firebrick manufacturer, we sincerely recommend Kerui Refractory. Not only are there high-standard products, but there are also a variety of options! Welcome to visit Kerui factory.