REFRACTORY CEMENT
As a kind of main aggregate, refractory cement is crucial in high temperature applications. The Al2O3 content of Kerui is about 50-81%, which brings excellent refractoriness and other performances. There are CA50, CA70 and CA80 cement for sale. The main difference is chemical composition.
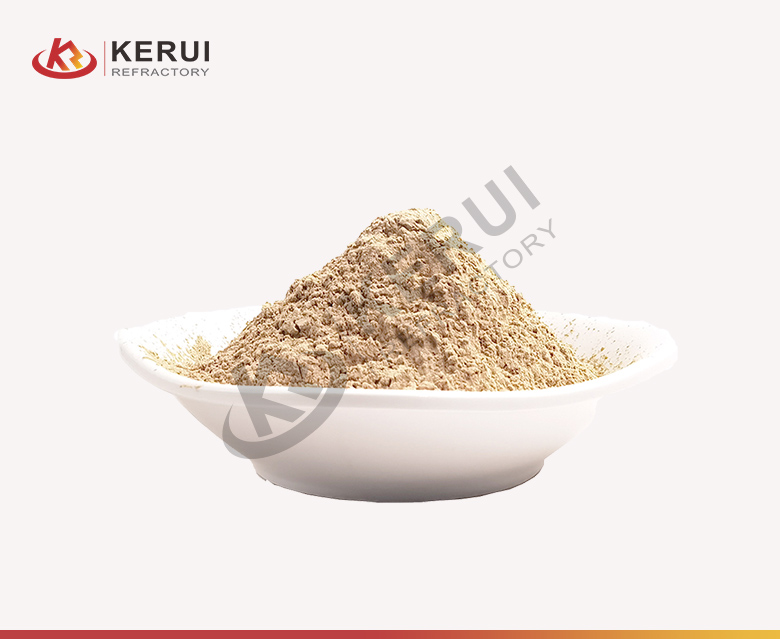
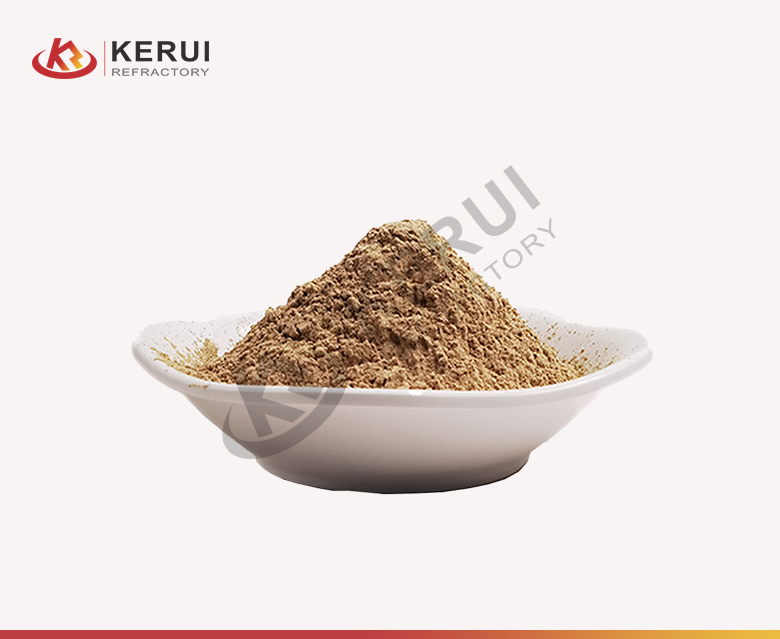
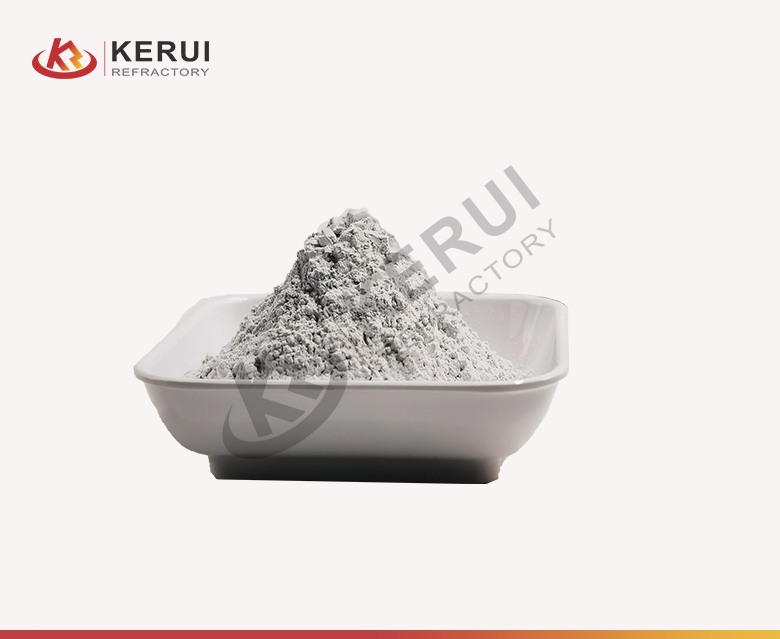
REFRACTORY CASTABLE
Refractory castable is easy to use with proper water. It’s suitable to pour, tamp, or vibrate into place to form a refractory shape or structure without the need for firing or baking. The bulk density is about 0.8-3.2 g/cm³, which can ensure safe and efficient production of your business.
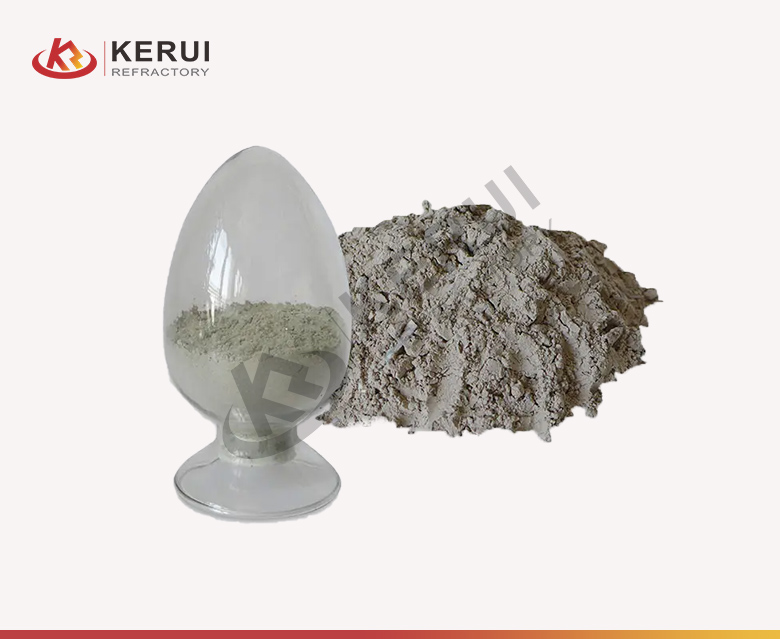
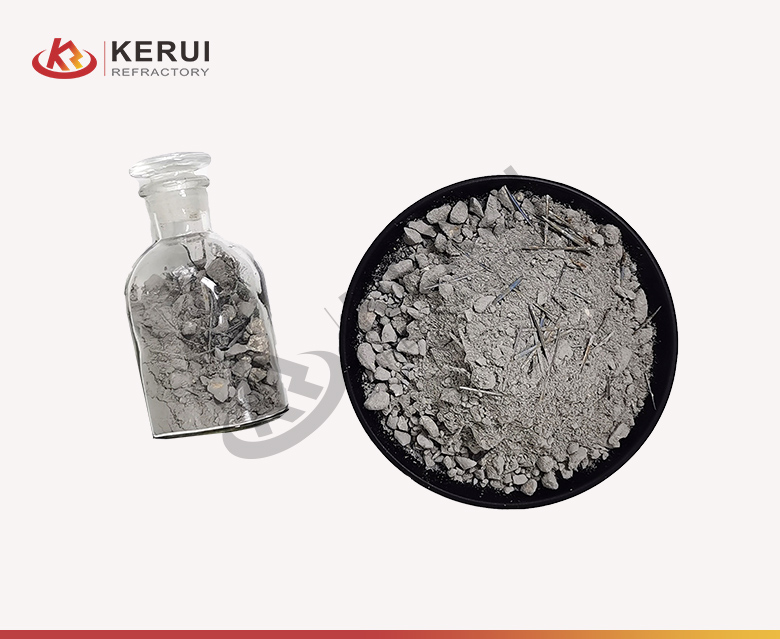
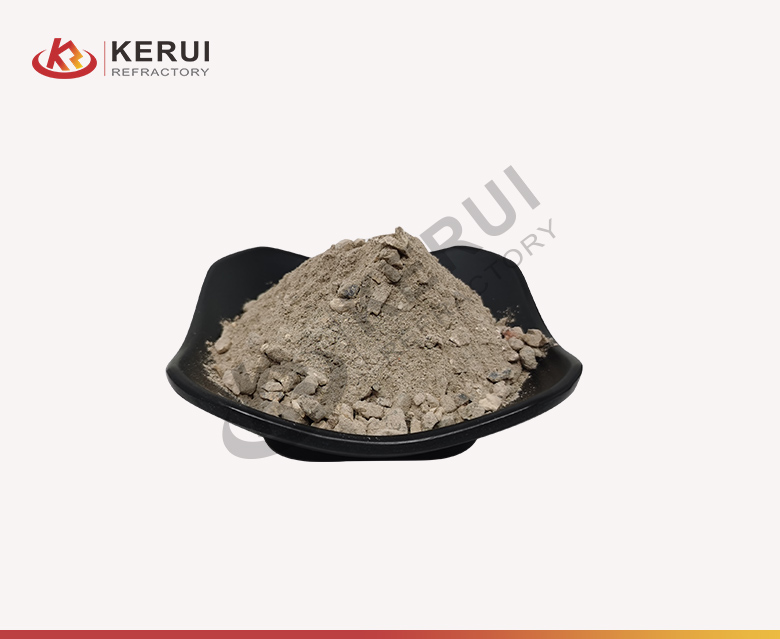
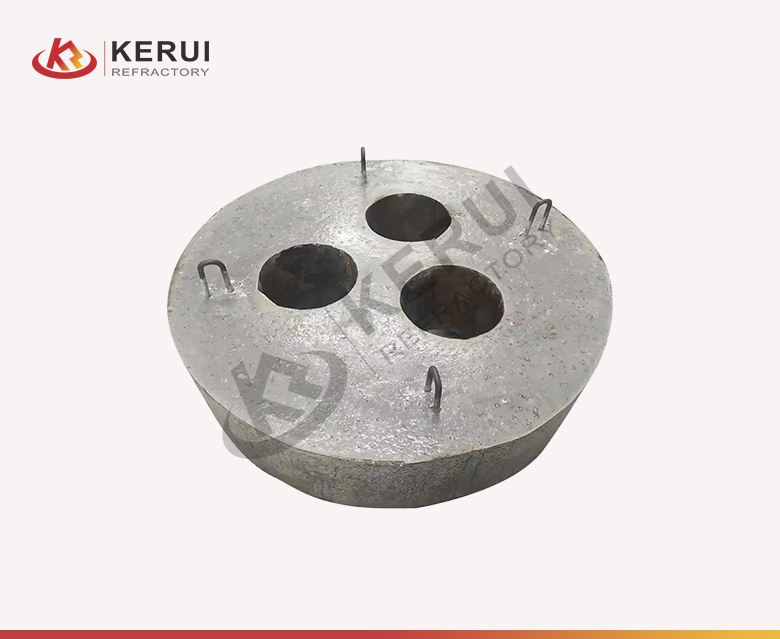
RAMMING MASS
Kerui refractory ramming mass is a granular or powdered refractory material that is dry mixed with a bonding agent and then rammed into place within a furnace lining using a ramming tool. The Al2O3 content is about 30-90%. Now use the ramming mass to create a dense and thermally stable lining for your kiln.
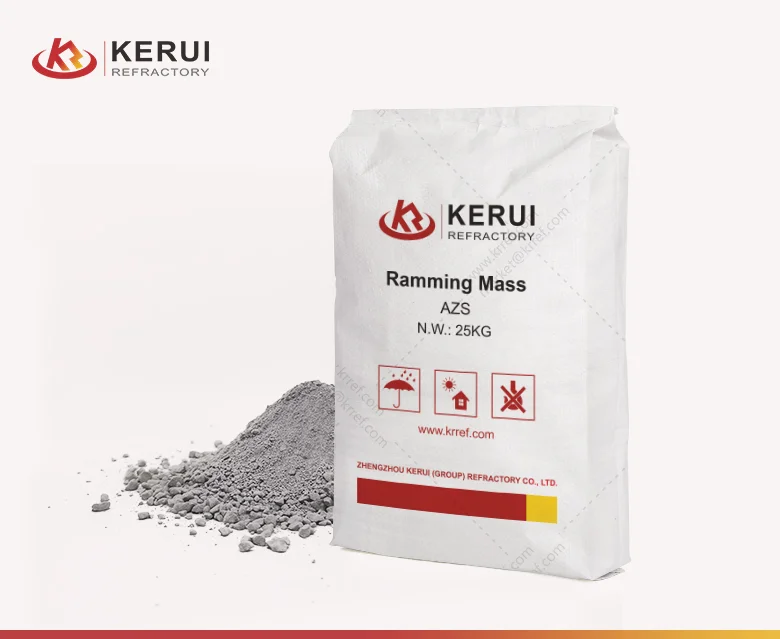
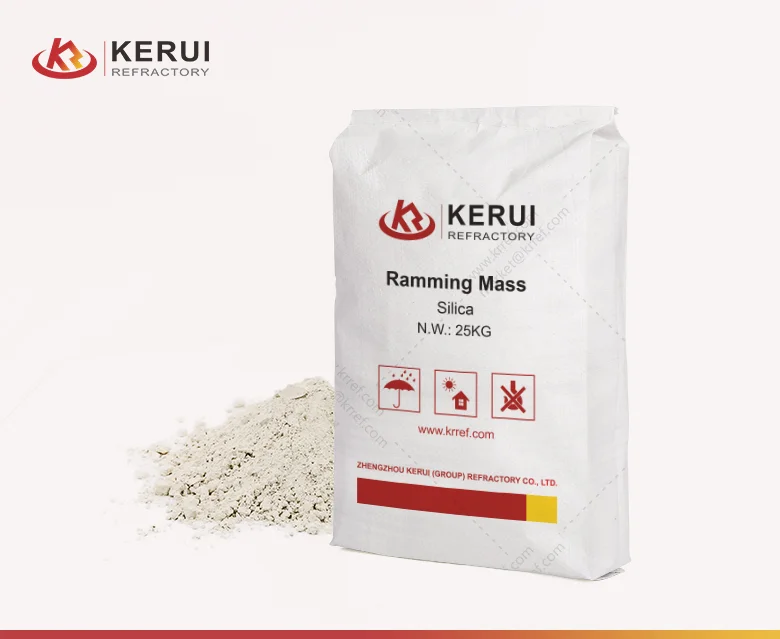
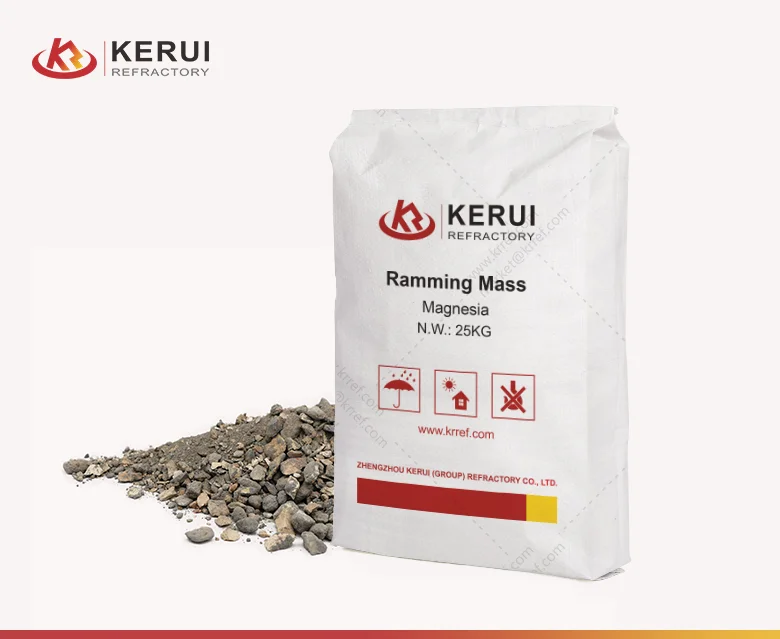
Applications of Kerui Monolithic Refractory Products
Ferrous industry: with special design, Kerui monolithic refractory products has extensive uses in blast furnaces, hot blast stoves, iron ladles, torpedo ladles and other key parts of steel and iron making industry.
Non-ferrous industry: Kerui monolithic refractory products are indispensable in crucial equipment like rotary kilns for calcination, converters, anode furnaces, and tundishes in aluminum smelters and copper refineries. Moreover, the excellent chemical resistance makes safe operation of operation of non-ferrous metal processing facilities.
Industrial Furnaces: Kerui monolithic refractory products are tailored for different parts of industrial furnaces, ensuring optimal performance in critical applications. In glass furnaces, these products are used in the crown, sidewalls, bottom and other parts. Besides, you may need this product in glass furnace, cement kiln, lime kiln and many other industrial furnaces and kilns.
Power station and other industries: Kerui monolithic refractory products play a vital role in power stations and various other industries. They are used in boilers, incinerators, gasifiers and fluidized bed reactors within power plants. Additionally, it has wide uses in diverse industries such as petrochemical, ceramics, environmentally friendly industries and so on.
KERUI Support for Monolithic Refractory Products
-
Production Support
The annual output of Kerui unshaped refractory materials is more than 50,000 tons! There are highly automated batching system and mixing system to realize efficient production. Besides, Kerui owns a large storage area. It’s available to require refractory cement or refractory castable in stock, which can promote your business greatly.
-
Delivery Support
Just as we mentioned above, the large stock of monolithic refractory products makes fast delivery available. Moreover, Kerui Refractory is able to delivery the customized refractory products in 7 working days. There is a responsible delivery team as well as international famous logistic company to ensure the safe and fast delivery of your monolithic products.
-
Technical Support
With more than 20 professional engineers in Kerui, you can enjoy technical guidance from the selection of monolithic products to the final construction and the following maintenance. They have rich project experience in more than 50 kinds of industrial high temperature kilns. To facilitate your business, Kerui Refractory offers both online guidance and on-site support.
-
Customization Support
As an original refractory products manufacturers in China, Kerui Refractory has a strong design and customization ability. Customers can send detailed requirement such as chemical composition, size, package terms and many other aspects. Kerui offers turnkey service which saves your time and effort.
Kerui Cases
Due to excellent quality of refractory products as well as professional service, Kerui has been the first choice of worldwide customers. Customers can enjoy professional assistant throughout each step of you business. Now Kerui customers cover more than 5 continents and 30 countries in the world, including Sri Lanka, Pakistan, Vietnam, Indonesia, South Korea, Iran, Syria, Turkey, Russia, Kazakhstan, Uzbekistan, Italy, United Kingdom, Germany, Seychelles, Egypt, Morocco, Canada, United States, Madagascar, Australia…
Kerui Partners
In the past decades, Kerui establishes stable partners. They come from famous enterprises from the industry and the world’s top 500 enterprises. Main partners of Kerui Refractory are RUSAL, ALBA, POSCO, SUNSTONE, CHALCO, EGYPTALUM, PSM, SONOCC, CNBMINTERNATIONAL CORP, XING DA STEEL CORD (THAILAND) COMPANY LIMITED, SHANDONG NANSHAN ALUMINIUM CO,. LTD. SHANDONG WEIQIAO VENTURE CO., LTD. and so on.
-
One-to-one ServiceExperienced International Sales Manager Provides One-to-one Service
-
Professional Solution30+ Technicians Offers Professional Solutions Based on Customers’ Site Conditions
-
Quality Management SystemQuality Management System Ensures the Stability of Products
-
Responsible After-sales ServiceRegular Customer Visit and Lifelong After-sales Service
FAQs About KERUI Monolithic Refractory Products
Here are some common questions and answers that customers may have regarding to monolithic refractory products:
- For common monolithic refractory products: 20 working days (immediate shipment in stock and 20 working days of shipment);
- For customized monolithic refractory products: 35 working days (5-7 working days of production and 30 days of shipment).
- Quality control point1: purchase of raw materials that are in line with purchase standards;
- Quality control point 2: control the fineness and granularity of raw materials;
- Quality control point 3: control the fineness, granularity and water content of mud materials;
- Quality control point 4: control the size of mold, presses and the bulk density, porosity as well as the single weight of per bags of monolithic refractory products;
- Quality control point 5: control the appearance and size, corners as well as density of monolithic refractory products;
- Quality control point 6: control different temperatures in the sintering kiln, including the drying zone, transition zone, sintering zone, cooling zone, etc;
- Quality control point 7: control the final products according to drawing, including sizes, corners, impurities and other aspects;
- Quality control point 8: conduct a comprehensive inspection of the final product in accordance with inspection procedures.